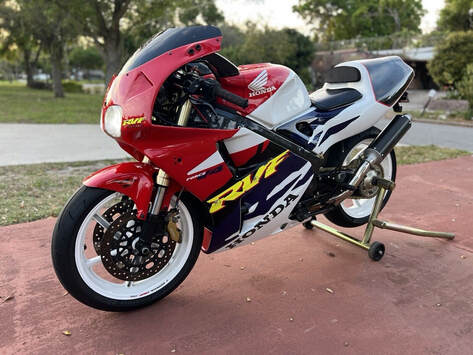
Why: Beautiful, desirable, rare
Where: Orlando, Florida
Price: Auction; BIN $11,500
Often referred to as a smaller sibling to the RC45 (previous post), this little screamer was only available in the Japanese market. This final iteration of the 400cc V4 was a comprehensive upgrade over the earlier VFR400. Production actually ended in 1996 but left-overs were available for a few more years, explaining this 1997 example.
And this one enjoys a sampling of modifications, including Tyga bodywork, Ducati rear wheel, several carbon fiber bits and more. Whether these changes make the bike more or less desirable is up to the buyer to decide, but the buy-it-now price of $11,500 is in line with more original examples. Note that there's no mention of the missing turn signals and mirrors.
If you're the appropriate size and have the required flexibility, then the RVF400 is reportedly among the finest handling and fastest in this class. According to MCN, "Honda at their very best."